Vacuum Heat Treatment Furnace
Vacuum Sintering Furnace
Vacuum Brazing Furnace
(The article comes from the Internet. If reprinting is not allowed, please contact our company to delete it.)
Please send us your inquiry about the customization of other furnace types or related questions about vacuum furnace. We will reply you immediately. Thank you.
Downloads
All documents in the overview
News & Press
All news at a glance
Request
Send us a message
Email: contact@vacfurnace.com
Tel : +86-21-50878190
Wechat : 2210154395
Address: NO.1299, XinJinQiao Road, Pudong New Area, Shanghai, China.
Copyright © 2010-2021 Shanghai Gehang Vacuum Technology Co.,Ltd. All Rights Reserved.
What is a carbide cutter?
CuW alloys are used where the combination of high heat resistance, high electrical and thermal conductivity, and low thermal expansion are needed. Some of the applications are in electric resistance welding, as electrical contacts, and as heat sinks. As contact material the alloy is resistant to erosion by electric arc. WCu alloys are also used in electrodes for electrical discharge machining and electrochemical machining.
Copper–tungsten (tungsten–copper, CuW, or WCu) alloy is a pseudo-alloy of copper and tungsten. As copper and tungsten are not mutually soluble, the material is composed of distinct particles of one metal dispersed in a matrix of the other one. The microstructure is therefore rather a metal matrix composite instead of a true alloy.
Copper tungsten material list :
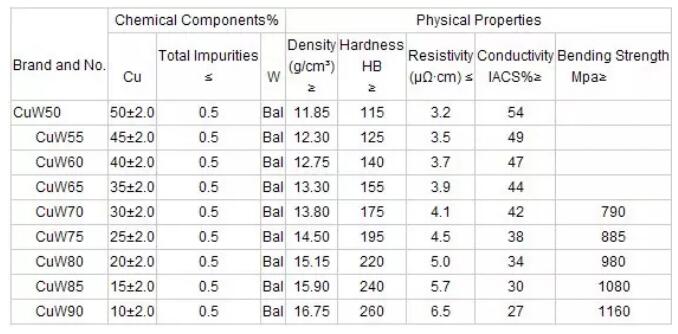
The material combines the properties of both metals, resulting in a material that is heat-resistant, ablation-resistant, highly thermally and electrically conductive, and easy to machine.
Parts are made from the CuW alloy by pressing the tungsten particles into a desired shape, sintering the compacted part, then infiltrating with molten copper. Sheets, rods and bars of the alloy are available as well.
Commonly used copper tungsten alloy contains 10–50 wt.% of copper, the remaining portion being mostly tungsten. The typical properties of the alloy depend on its composition. The alloy with less wt.% of copper has higher density, higher hardness and higher resistivity. The typical density of CuW90 alloy, with 10% of copper, is 16.75 g/cm3 and 11.85 g/cm3 for CuW50 alloy. CuW90 has higher hardness and resistivity of 260 HB kgf/mm2 and 6.5 µΩ.cm than CuW50.
What are the uses of tungsten-copper alloy?
A large part of tungsten-copper alloy is used in aerospace, aviation, electronics, electric power, metallurgy, machinery, sports equipment and other industries.Secondly, it is also used to manufacture contacts of high-voltage electrical switches that are resistant to arc ablation, rocket nozzle throat lining, tail rudder and other high-temperature components. It is also used as electrodes for electrical processing, high-temperature molds and other occasions requiring conductive and thermal conductivity and high-temperature use.
Process Technology
The technological process of w – cu alloy:
Powder process—Material Allocation—Press Formation—Sintering&Soluble Permeability—Cold working.
1. Mixed w/cu or mo/cu powder is pressed into shape and sintered at 1300-1500° liquid phase.
The material prepared by this method has poor uniformity and more closed voids.its density is usually less than 98%, but the sintering activity can be improved by adding a small amount of nickel to the preparation of ultrafine and nanometer powders by the activation sintering method, mechanical alloying method or oxide supply reduction method, so as to improve the density of tungsten-copper and molybdenum-copper alloys.However, nickel activation sintering can significantly reduce the conductivity and thermal conductivity of the material, and the introduction of impurities by mechanical alloying can also reduce the conductivity of the material.The process of preparing powder by oxide co-reduction is complicated and the production efficiency is low.
2. Injection molding (hydrogen sintering)
High – density tungsten alloy was prepared by injection molding.Its manufacturing method is uniform particle size of 1-5 micron copper nickel powder, tungsten powder or iron powder with particle size of 0.5-2 micron tungsten powder and tungsten powder mixing, 5-15 microns again in 25% 30% of organic binding agent (such as paraffin wax or poly (methyl acrylic vinegar), injection molding, steam cleaning and ZhaoSheFa except to adhesive, sintered in hydrogen, for high-density tungsten alloy.
3. Copper oxide powder method
Instead of using copper oxide powder (which is mixed and ground down to copper), copper forms a continuous matrix in the sintered press, and tungsten serves as a reinforced frame.The high expansion component was restricted by the second component in the four weeks, and the powder was sintered in the wet hydrogen at a lower temperature.According to the introduction of a very fine powder can improve the sintering performance and densification, so that it can reach more than 99%.Tungsten and molybdenum skeleton melting method
The tungsten powder or molybdenum powder is first pressed into shape and sintered into a tungsten and molybdenum skeleton with a certain porosity.
This method is suitable for tungsten copper and molybdenum copper products with low copper content.Compared with tungsten copper, molybdenum copper has the advantages of small mass, easy processing, linear expansion coefficient, thermal conductivity and some main mechanical properties comparable to tungsten copper.
Although its heat resistance is not as good as that of tungsten and copper, it is better than that of some heat resistant materials.Because the wettability of molybdenum-copper is worse than that of tungsten-copper, especially when preparing molybdenum-copper with low copper content, the density of the material after melting is low, resulting in the material’s air tightness, electrical conductivity, thermal conductivity can not meet the requirements, and its application is limited.
SIMUWU high vacuum sintering furnace is mainly used for cemented carbide, powder stainless steel, magnetic materials, special ceramics, refractory metals and alloys (tungsten, molybdenum,
The degreasing and sintering of tungsten and copper alloys.Degreasing, pre-firing, sintering and rapid cooling can be realized in the same furnace.The production process is completed in one time, greatly improving the production efficiency and product quality.Low pressure sintering can be carried out under the protection of argon, nitrogen and reductive gas separation to reduce the loss of element volatiles.Directional pressure flow degreasing, enhance degreasing effect, no hidden fat corner in the furnace, degreasing more complete.
Edited by: Lucky Hu
Copyright: SIMUWU Vacuum Furnace
Related products:
Hydrogen vacuum sinteing furnace
Tungsten sintering furnace