Vacuum Heat Treatment Furnace
Vacuum Sintering Furnace
Vacuum Brazing Furnace
(The article comes from the Internet. If reprinting is not allowed, please contact our company to delete it.)
Please send us your inquiry about the customization of other furnace types or related questions about vacuum furnace. We will reply you immediately. Thank you.
Downloads
All documents in the overview
News & Press
All news at a glance
Request
Send us a message
Email: contact@vacfurnace.com
Tel : +86-21-50878190
Wechat : 2210154395
Address: NO.1299, XinJinQiao Road, Pudong New Area, Shanghai, China.
Copyright © 2010-2021 Shanghai Gehang Vacuum Technology Co.,Ltd. All Rights Reserved.
Brazed diamond tool
1 Metal Binder Diamond Tool
According to different manufacturing methods, metal bonded diamond tools can be divided into three categories: powder metallurgy hot pressing sintered diamond tools, electroplated diamond tools and brazed diamond tools.
1.1 Powder Metallurgy Hot Pressing Sintering Diamond Tools
Powder metallurgy hot pressing sintering diamond tool is a kind of diamond tool product, which is made of diamond as cutting and grinding material, metal powder as binder, powder metallurgy method, through mixing, granulation, pressing, sintering and necessary post-dressing.
Products have formed a series of standardization, complete varieties and specifications, product quality is stable, some products have a certain competitiveness in the international market. Powder metallurgy hot-pressing sintered diamond tools are the earliest type of diamond products. They are also the most widely used diamond tools with the largest variety, the largest amount and the widest use. The sales volume of products accounts for more than 80% of the total metal bonded diamond tools.
Although the diamond tools produced by this method have been widely used in various industries and achieved remarkable economic benefits, the technology of consolidating diamond abrasive particles has always had serious shortcomings. The effective utilization rate of diamond is about 10%, which results in a great waste of diamond abrasive resources. The main manifestation is that diamond abrasives exist in metal matrix in the form of mechanical encapsulation. Metal binder has weak control over diamond abrasives. There are more abnormal wear, peeling and residual diamonds in the use of diamond tools. The actual utilization rate of diamond is low, and the waste of diamond raw materials is large.
Over the years, experts in the industry have done a lot of work to improve the holding capacity of metal bonds on diamond. In addition to improving the holding capacity of metal bonds on diamond abrasives by surface modification (surface metallization, surface morphology change, etc.), metal bonds can be directly added with appropriate amounts of Ti (Ti), Cr (Cr), In (In). There is no big breakthrough in strengthening metal bonds by active elements such as Zr (zirconium). It is generally believed in academia that the strengthening mechanism of metal bond is to form a layer of metal carbide between the diamond surface and the bond, and use the carbide as the transition layer to improve the wettability and capillarity of the bond on the diamond surface, so as to achieve the effect of chemical metallurgy bonding.
In fact, in order to protect diamond abrasives from graphitization and affect the quality of diamond, the sintering temperature of diamond abrasives can not reach the melting temperature of these active elements and carbides can not be formed during hot pressing sintering, which leads to the inadequacy of active elements in theory. Diamond Abrasives have to be mechanically clamped in metal bonds, and there is no so-called chemical metallurgical reaction. Therefore, this kind of tool only depends on the form of mechanical encapsulation to fix the diamond abrasive, and the control of diamond in the use process is limited.
Observing the use of a large number of powder metallurgy hot-pressing sintered diamond tools, it is found that the chip-holding space of diamond abrasives is formed in the process of operation, which is obtained by the back-grinding of the waste materials. The chip-holding space of diamond abrasives is a process from scratch, so the average value of the chip-holding space of diamond abrasives is very small during the effective use of diamond abrasives. In the use process, the phenomenon of blocking and burning and scratching the workpiece by the processing material scraps often occurs.
1.2 Electroplated Diamond Tools
Electroplated diamond tool is a kind of product which is firmly embedded on the metal matrix by electroplating and metal electrodeposition process. This kind of products has the characteristics of high efficiency and high grinding precision. The main products are forming grinding and precision processing tools. The products are also widely used in geological exploration, stone, machinery, automobile and national defense industries.
Although all kinds of diamond tools produced by this method have been widely used in a certain industry and achieved certain economic benefits, there are serious shortcomings in the consolidated diamond abrasive technology itself. The effective utilization rate of diamond is about 20%. The main manifestation is that the metal bond is not strong enough to control the diamond abrasive particles, and the diamond abrasive particles are only embedded in the coated metal by mechanical embedding.
The method of electroplating is that Ni or Ni-Co or Ni-Co-Mn metal ions continuously precipitate, enter and bury on the surface of cathode diamond and matrix, and the next electroplating layer is deposited in turn. After repeated deposition to a certain thickness, semi-finished products are taken out from the electroplating bath for subsequent processing, such as sanding and thickening, and finally electroplated diamond tools are obtained. During the whole manufacturing process, no chemical metallurgical reaction took place in diamond. Therefore, this kind of tools only rely on mechanical wrapping to fix diamond abrasives. The control of diamond is limited in the use process. Once the electroplating layer is worn to half the height of abrasives, the diamond abrasives will fall off naturally.
Observing the use of a large number of electroplated diamond tools, it is found that about two-thirds of the undissolved diamond abrasives are deposited in the electroplated metal layer, so the chip-holding space of diamond abrasives is basically fixed and relatively small, so the phenomenon of blocking and burning the workpiece by processing material scraps will still occur in the use process.
1.3 Brazing Diamond Tools
Brazing diamond tool is a tool product which solders a layer of diamond firmly on the metal matrix through the melting process of metal solder. This kind of products has the characteristics of higher efficiency, long service life of single diamond particle and high grinding accuracy. The main products cover all coarse and medium-sized electroplated diamond tools and some hot-pressed diamond tools.
In order to avoid the problems of low holding power, small chip space, low exposure height and easy falling off caused by traditional manufacturing methods, and to make greater use of the advantages of single-layer diamond tools, brazing technology has been applied to the field of diamond tools manufacturing since 2000 and has developed rapidly. Brazing technology, as a new manufacturing method of diamond tools, has attracted wide attention all over the world. Different from other welding methods, the melting temperature of brazing alloy is lower than that of base metal, and the brazing temperature is lower than that of solid phase and higher than that of liquid phase. For diamond, brazing temperature is lower than graphitization transition temperature of diamond. During brazing, the filler metal wets, capillarizes, fills, spreads and wraps diamond abrasives tightly on the surface of diamond. At the same time, the chemical metallurgical bonding between diamond and filler alloy is formed in the form of carbide. The diamond tools manufactured by brazing method have higher bonding strength of diamond abrasive grains and higher cutting edge height, improved sharpness and cutting performance, fixed chip space and relatively large, especially suitable for high-speed and high-efficiency grinding, processing of difficult-to-process materials and precision processing. In recent years, brazing single-layer diamond tools at high temperature has become a research and development hotspot for research institutes and manufacturers in universities.
2 Brazing Diamond Tool Technology
Since 2000, experts and scholars in China have made extensive technical research and new product development in brazing diamond tools. Great progress has been made in brazing technology and equipment manufacturing, brazing alloy powder manufacturing and brazing tool performance research and production.
2.1 Brazing Technology and Equipment Manufacturing
In order to meet the development of brazing diamond technology, SIMUWU has developed a special high vacuum brazing furnace for diamond tools and its operation technology, as well as induction heating welding equipment, to meet the needs of brazing diamond tools technology.
2.2 Manufacture of Brazing Alloy Powder
Brazing alloy powder is the key of brazing diamond technology.
The manufacturing principles of brazing alloy powder are as follows:
(1) The brazing alloy has good wettability to diamond and metal matrix, and low wettability angle.
(2) The solder alloy has good ductility.
(3) The brazing alloy has good climbing ability, which makes the diamond have enough protruding height and good chip capacity.
(4) Effective metallurgical-chemical bonding between solder alloys and diamond surface produces the strongest carbide structure and the most reasonable carbide thickness, which makes it have good control over diamond.
(5) The brazing alloy should have lower melting point to reduce brazing temperature and thermal damage to diamond.
(6) The cost of solder alloys should be lower, which is helpful to reduce the cost of brazing tools.
SIMUWU experts and scholars have carried out a long-term research and development of brazing alloy powder, and now developed a proprietary diamond tool brazing alloy powder. They are:
(1) Silver-based solder. It is mainly composed of Ag-Cu-Ti. Because of its lowest melting point temperature, best wettability and ductility, it is often used to weld tool products and precision fine diamond single crystal, CBN, PCD high-tech products.
(2) Copper-based solder. Mainly composed of copper-Sn-Ti, because of its low melting point temperature, good wettability and ductility, it is often used to weld diamond with lighter load, CBN products and more precise fine-grained diamond, CBN high-tech products.
(3) Nickel-based solder. It is mainly composed of Ni-Cr. Because of its high melting point temperature, good wettability and ductility, it is often used to weld heavy-duty diamond and cemented carbide products.
2.3 Brazing Tool Performance
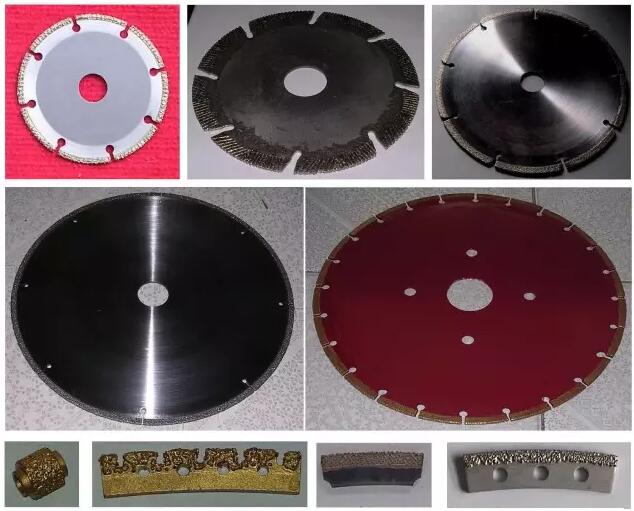
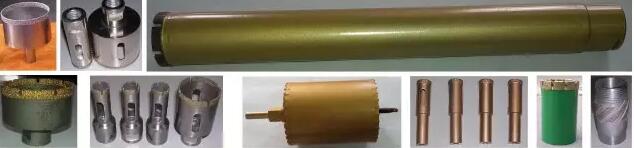
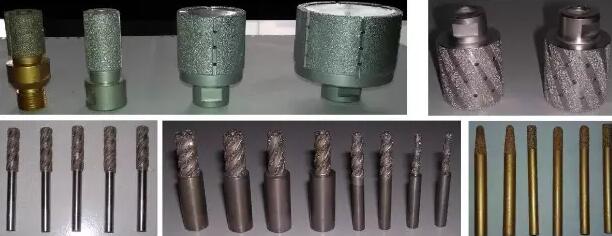

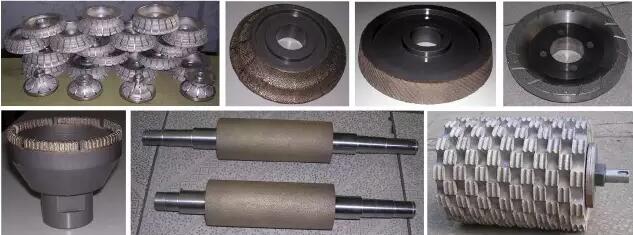
SIMUWU experts and scholars in the development of diamond technology equipment and brazing alloy powder at the same time, in-depth research and production of diamond cutting tools, diamond drilling and milling tools and diamond grinding tools, in a number of processing areas have been applied, and achieved certain experience and economic benefits.
(1) Cutting tools
At present, brazing cutting tools developed and produced involve marble, concrete, metal castings, composite materials and other processing fields.
(2) Drilling and milling tools
At present, brazing drilling and milling tools developed and manufactured involve glass, stone, concrete, metal, composite materials, geology and other processing fields.
(3) Grinding tools
At present, brazing grinding tools developed and manufactured involve a wider range of processing areas and the largest variety.
3. Problems in brazing diamond technology
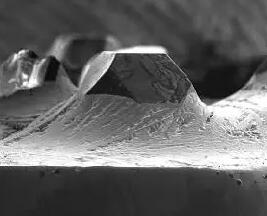
3.1 Achievements and Progress of Brazing Diamond Technology
After more than ten years of industrial development, brazing diamond technology has made the following technological achievements or progress:
(1) Fully grasp the brazing mechanism of diamond
The mechanism of diamond brazing has been studied. The principle of brazing diamond tools is to use carbide-forming elements (such as Ti, Cr, Zr, V, W, etc.) as brazing filler metals to react with the surface of diamond during brazing process and form a layer of carbide at the interface. With the help of this layer of carbide, melting, soaking and infiltration occur at the interface of diamond, brazing filler metal and matrix. The interaction of diffusion and chemical bonding can be achieved by brazing to achieve a solid chemical-metallurgical bonding, and to achieve the holding strength of the filler metal to the matrix and the diamond abrasive particles.
At the same time, in order to improve the holding power of diamond abrasive and effective cutting space, and give full play to the technical characteristics of brazing diamond, experts have also completed a comprehensive study on the carbide morphology formed on the surface of diamond by various solders (nickel-based solder, copper-based solder, silver-based solder, etc.) at different temperatures and holding time, and determined the diamond surface. The carbide morphology and reactant thickness with the strongest holding power of the diamond and the best diamond particle morphology after welding are obtained.
(2) The production of low temperature solder has been realized.
In order to reduce the thermal damage of diamond in brazing process, without reducing the holding power of filler metal on matrix and diamond abrasive, experts in the industry have completed the research and development of low-temperature brazing filler metal for diamond welding, realized the large-scale production of low-temperature brazing filler metal, and greatly reduced the damage to diamond in brazing process.
(3) Improve the production process system of brazed diamond tools
At present, the high vacuum brazing furnace and its brazing technology have been very mature. Induction brazing technology is also being improved.
(4) The structure of tools has been given enough attention.
There have been many research results on tool structure, such as regular and uniform distribution of diamond grits, uniform feeding of diamond grits, equal thickness beach, linear distribution of sand, array distribution of sand, strip distribution of sand and block distribution of sand, which can withstand heavy loads.
(5) The adaptability of tools is becoming more and more professional
For the processing of glass, stone, concrete, metal, ceramics, plastics, rubber, composite materials and so on, a suitable tool manufacturing technology has been developed.
3.2 Problems in Brazing Diamond Technology
Although brazed diamond technology has a certain market after more than ten years of development, there is still a technical problem that “compared with powder metallurgy sintered diamond tools, the service life of brazed diamond tools is relatively low”, which seriously restricts the development of brazed diamond technology.
Powder metallurgy hot-pressing sintering diamond tools are multi-layered, so their service life is relatively long, but the utilization rate of diamond abrasives in these tools is relatively low, less than 10%. The mechanism in the use process is that after a period of time, the edge of the edged diamond becomes blunt and the cutting force acting on the abrasives becomes larger, as the cutting force used on the abrasives is greater than that used on the abrasives. When the grinding force is in control, the abrasive peels fall off, and the next layer of diamond pellets come out. After the new diamond pellets come out, they continue to undertake cutting work. Therefore, the long service life of metal bonded diamond tools is guaranteed because of the succession of diamond abrasives.
The brazed diamond tools are mainly single-layer, but they have a relatively high grinding capacity for diamond abrasives, a relatively long service life and a relatively high utilization rate for diamond, but no matter how the brazed diamond tools are used, there is only one layer of diamond, and their service life is relatively short compared with the overall tools.
Through a lot of experiments, we find that two main causes of failure of brazed diamond tools have not been solved, and these two reasons directly affect the service life of brazed diamond tools.
One is that the diamond abrasives produced on the market at present are lack of micro-fragmentation. After a period of use, the edges and corners of diamonds can only be ground round without small fragments, thus losing their sharpness, resulting in tool failure due to loss of working ability. The second is that the matrix of brazing alloy itself can not withstand long wear and tear, and the tool can be brazed after a period of use. When the matrix is reduced to the extent of losing support for diamond abrasives, the diamond abrasives will fall off and the tools will lose their working ability and fail.
However, we believe that by solving the self-sharpening of diamond and the wear resistance of brazing filler metal, the service life of brazed diamond tools can continue to be improved, and there is theoretically five times more room for improvement. Therefore, improving the service life of brazed diamond single layer diamond is one of the important topics that need to be further studied in brazed diamond technology.
4 Conclusion
In order to further improve the brazed diamond technology, we need to closely combine the wear resistance, compactness and metallurgical properties of brazed alloys. The following studies are carried out to improve the service life of brazed diamond tools.
(1) Exploring the technology of self-sharpening diamond production after treatment
We very much hope to produce sharpened diamond abrasives directly by high temperature and high pressure synthesis technology, but there is no successful production process of self-sharpening diamond in the actual production system, so it is impossible to purchase sharpened diamond abrasives directly from the market. So can the current diamond abrasive be transformed into self-sharpening by post-processing? We think it’s possible. So we need to study the diamond abrasives and find out the post-processing method through the self-sharpening of diamond abrasives.
(2) Analyzing the alloy characteristics and mechanism of various metals, and re-developing new brazing filler metals.
By analyzing the reaction effect of various metals in the brazing alloys, especially in the melting state and the mechanism of performance change, new brazing alloys with different materials are reconfigured, which lays a foundation for further improving the performance of diamond tools.